Latest wirewound resistor specification sheet
Mainstream Production Process of Wound Resistors
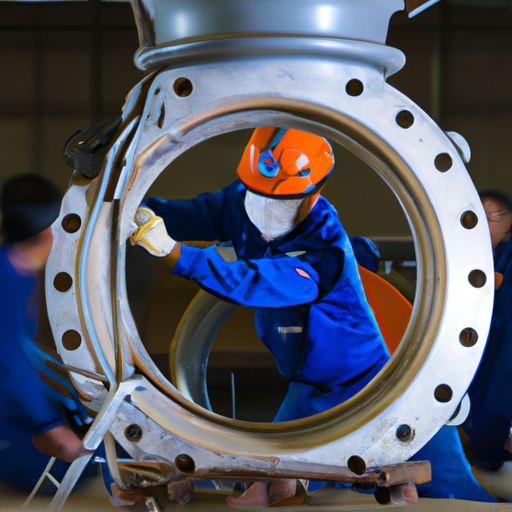
1. Material Preparation The main materials for wound resistors include resistance wire, insulating material, and terminals. The resistance wire is usually made of nickel-chromium alloy or copper-nickel alloy, with high resistivity and stability. Insulating materials typically include glass fiber cloth or ceramics, providing good insulation and high-temperature resistance. Terminals are usually made of copper or aluminum materials for circuit connections.
2. Winding First, the resistance wire is wound into a spiral coil according to design requirements, and then the coil is fixed on the insulating material. It is important to ensure uniform coil density and complete insulation material wrapping during winding to ensure the stability and durability of the resistor.
3. Welding The wound coil is welded to the terminals to form circuit connections. Welding requires controlling the welding temperature and time to avoid overheating or insufficient heating, which could result in weak welding or damage to the resistor.
4. Encapsulation The welded resistor is placed in a packaging mold, and insulating material is injected or insulating varnish is applied to form a protective shell for the circuit. The encapsulation process needs to ensure the sealing and corrosion resistance of the shell to ensure the stability of the resistor in harsh environments.
5. Testing The produced resistors undergo performance tests such as resistance value, voltage resistance, and temperature resistance to ensure they meet design requirements. The testing process needs to be precise and reliable to guarantee product quality and performance.
The production process of wound resistors requires strict control at every step to ensure product quality and performance. As electronic devices continue to evolve, the production process of wound resistors is constantly innovating and improving to meet market demands and technological advancements. It is hoped that through the above introduction, everyone can gain a better understanding of the mainstream production process of wound resistors, providing reference and guidance for the manufacturing of electronic devices.
Mainstream Production Process of Wound Resistors
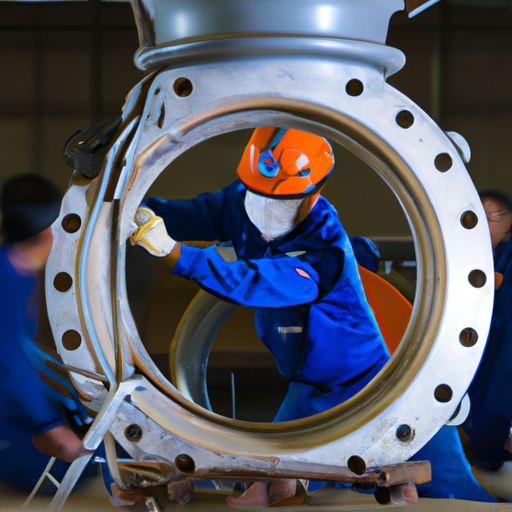
1. Material Preparation The main materials for wound resistors include resistance wire, insulating material, and terminals. The resistance wire is usually made of nickel-chromium alloy or copper-nickel alloy, with high resistivity and stability. Insulating materials typically include glass fiber cloth or ceramics, providing good insulation and high-temperature resistance. Terminals are usually made of copper or aluminum materials for circuit connections.
2. Winding First, the resistance wire is wound into a spiral coil according to design requirements, and then the coil is fixed on the insulating material. It is important to ensure uniform coil density and complete insulation material wrapping during winding to ensure the stability and durability of the resistor.
3. Welding The wound coil is welded to the terminals to form circuit connections. Welding requires controlling the welding temperature and time to avoid overheating or insufficient heating, which could result in weak welding or damage to the resistor.
4. Encapsulation The welded resistor is placed in a packaging mold, and insulating material is injected or insulating varnish is applied to form a protective shell for the circuit. The encapsulation process needs to ensure the sealing and corrosion resistance of the shell to ensure the stability of the resistor in harsh environments.
5. Testing The produced resistors undergo performance tests such as resistance value, voltage resistance, and temperature resistance to ensure they meet design requirements. The testing process needs to be precise and reliable to guarantee product quality and performance.
The production process of wound resistors requires strict control at every step to ensure product quality and performance. As electronic devices continue to evolve, the production process of wound resistors is constantly innovating and improving to meet market demands and technological advancements. It is hoped that through the above introduction, everyone can gain a better understanding of the mainstream production process of wound resistors, providing reference and guidance for the manufacturing of electronic devices.